A Leading Middle East Oilfield Development Company
Enhanced Equipment Management With RFID
In the oil and gas industry, asset management has always played a crucial role in maintaining
productivity and efficiency. One leading oil company from the Middle East, actively involved in
hydraulic fracking, faced multiple challenges managing their fracking iron and related high-value
equipment. This oil and gas-based company was operating on an outdated SAP system that
lacked the capability to track critical assets in real-time. Their manual tracking process led to
frequent delays, misplacements, and inefficient workflows.
After assessing their challenges, Silent Infotech proposed customized Odoo solutions with an
interactive dashboard. The proposed system featured RFID-based asset tracking integrated
seamlessly into an Odoo dashboard. This interactive dashboard served as a centralized hub for
all the data and information, making it easy for the team to access and manage all data from a
single screen.
What Were The Issues Faced By The Oil & Natural Gas Company?
As their operations were expanded across multiple locations, the company faced numerous
challenges :
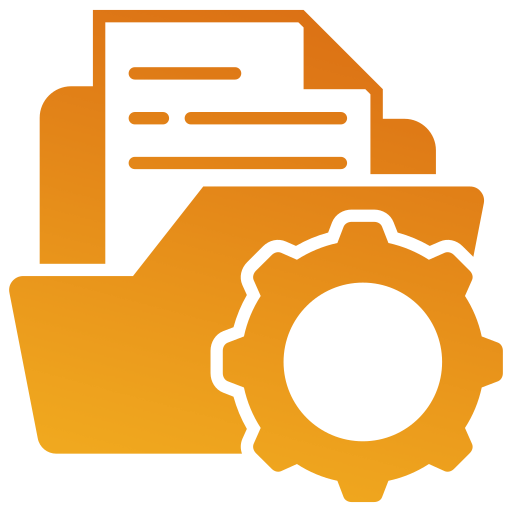
Equipment Mismanagement
leads to asset loss, inaccurate records, and delayed
maintenance.
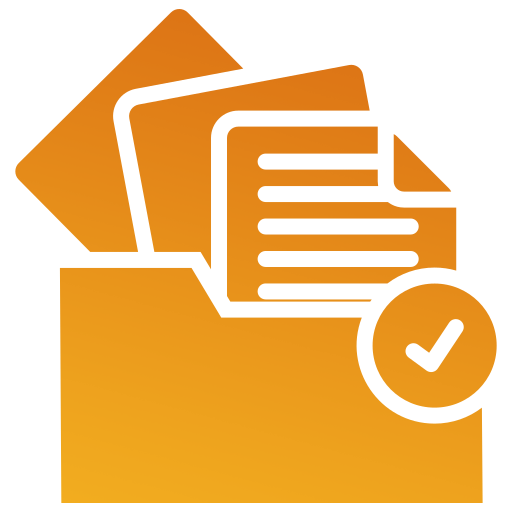
Inaccurate Manual Records
leads to data errors, misinformed decisions, and
operational inefficiencies.
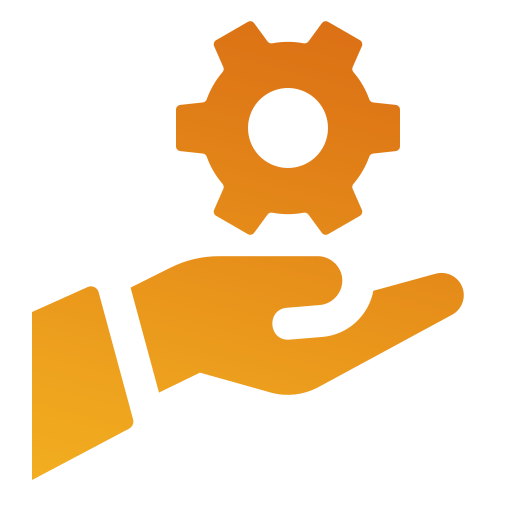
Delayed Servicing of Fracking Iron & Pumps
leads to equipment downtime and
reduced performance.
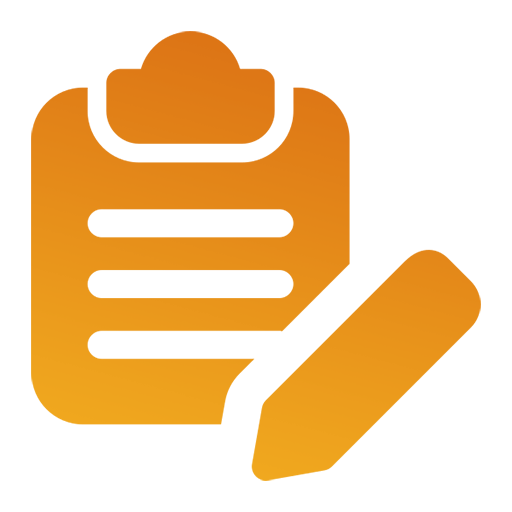
Compliance Record Issues
Results in regulatory penalties, and increased audit risks.
Get FREE Consultation
How Silent Infotech Helped Them Out With an Odoo-Based RFID Asset Tracking System?
RFID Tags
Durable, weather resistant RFID tags were attached to each fracking-iron
equipment, pumps, and other valuable assets, ensuring long-lasting performance.
RFID Readers & Gateways
RFID readers were placed at exits/entry points and
scanners were placed at field sites, used for real-time check-in/check-out tracking.
RFID - ERP Integration
The RFID-based system was integrated with Odoo ERP,
enabling real-time tracking of fleet and equipment. We migrated all data from an
outdated SAP system to Odoo.
Benefits of Silent Infotech Odoo based RFID implementation
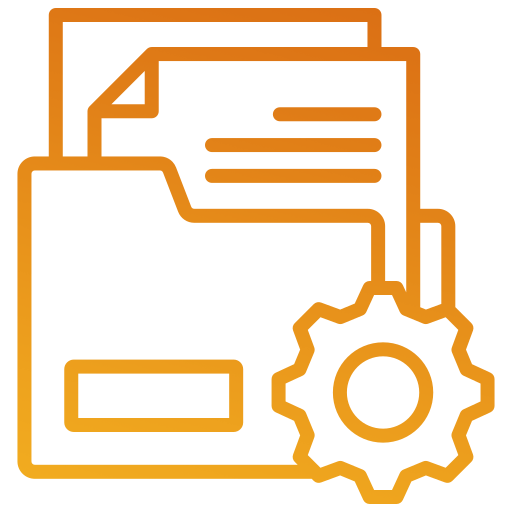
Project Management & Job Costing
Enabled better control over project budgets
with live costing insights, resource allocation, and progress tracking from a centralized
dashboard.
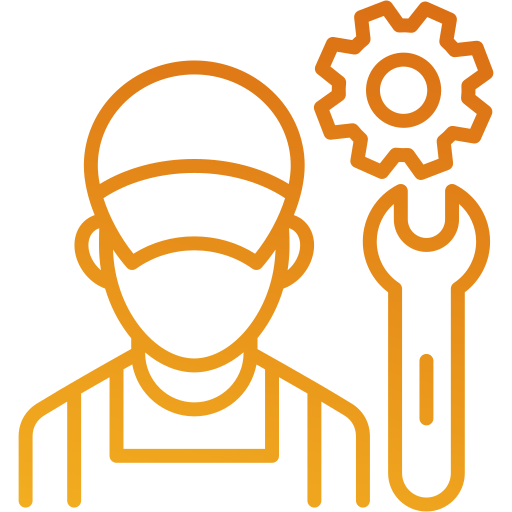
Advanced Maintenance & Planning
It ensures timely equipment servicing and
extends asset life. With advanced maintenance and planning, businesses can cut maintenance
costs, prevent failures, and improve operational efficiency.
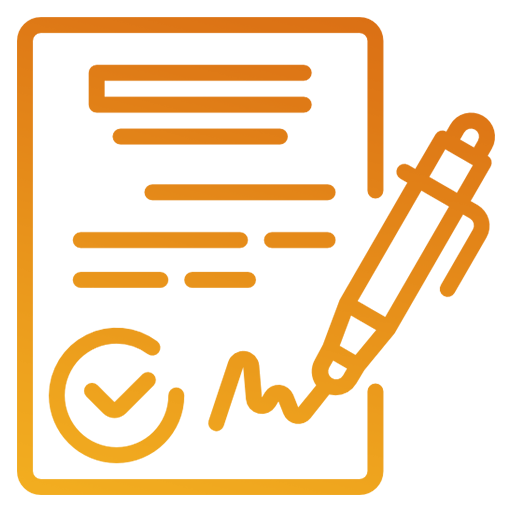
Contract & Lease management
Simplified the process of managing asset leases,
renewal schedules, and contract documentation within the ERP, improving compliance and
reducing missed deadlines.
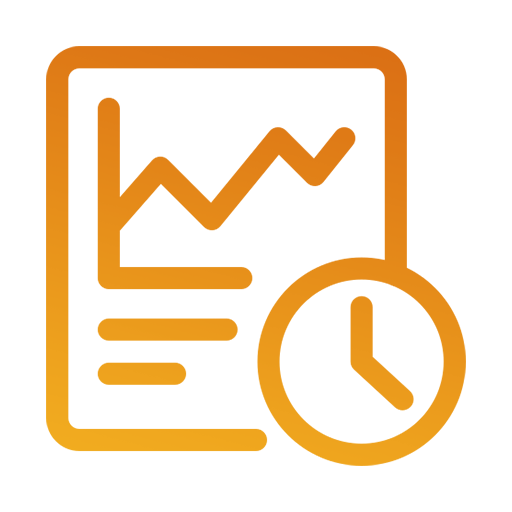
Real-time Asset visibility
Accurate tracking of the exact location, movement, and
utilization of fracking irons, pumps, and other high-value equipment across field sites using
RFID and ERP integration.
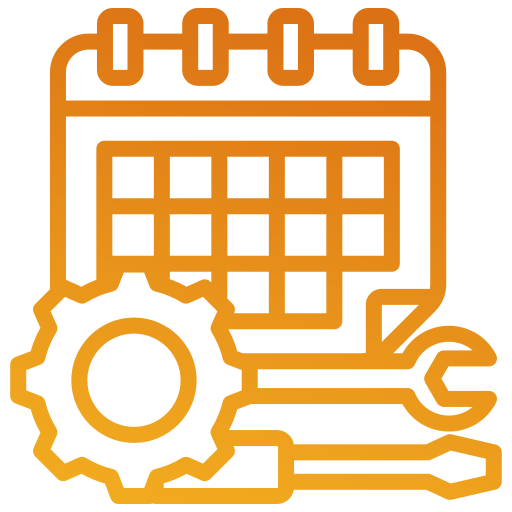
Proactive Maintenance Scheduling
The system now triggers automated
maintenance alerts based on usage and predefined intervals, reducing downtime
and extending asset lifespan.
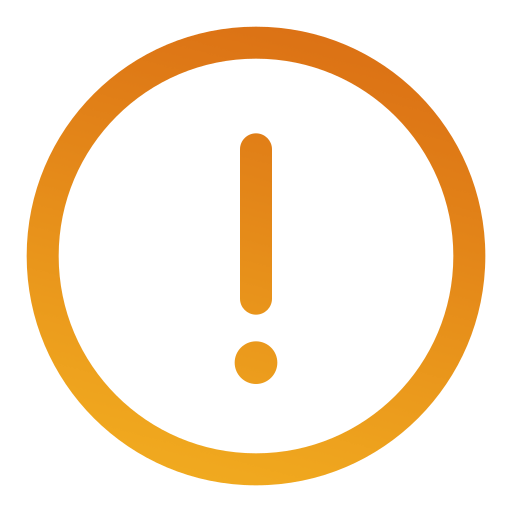
Error-Free Operations
Eliminated manual data entry and paperwork, significantly
reducing human errors in asset records, maintenance logs, and field crew task updates.
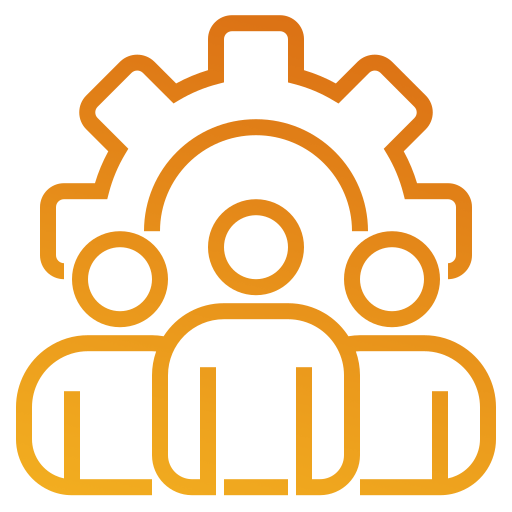
Field Crew Management
Mobile app access enabled field workers to check-in/out
assets, receive task updates, and report in real-time, boosting on-site efficiency and
response times.
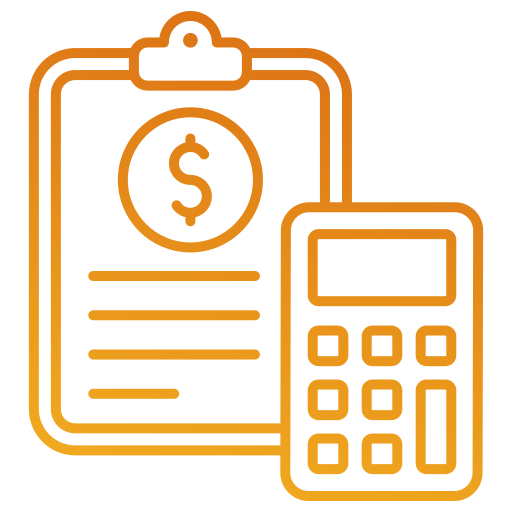
Streamlined Project Costing
Enabled better control over project budgets with live
costing insights, resource allocation, and progress tracking from a centralized dashboard.
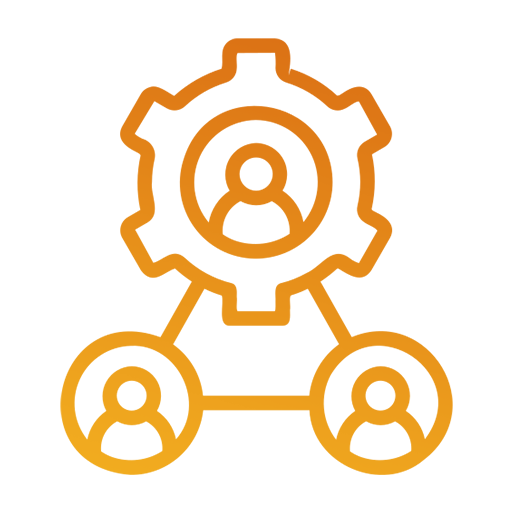
Interdepartmental Coordination
Enhances communication, streamlines workflows,
and accelerates decision making. It promotes collaboration across the teams and
organization-wide project execution.
Losing Track of High-value Equipment?
Get real-time asset tracking like this energy leader did.
Outcome Oilfield Development Company Experience After ERP Implementation
40%
boost in asset visibility, less misplacement & improved tracking.
30%
savings in asset management costs, through smarter inventory control.
25%
enhancement in operational efficiency, no risk of manual errors, and automated
workflows.
25%
reduction in audit risks, with accurate compliance reporting.
Conclusion
By optimizing Odoo + RFID technology, the company transformed its asset
tracking and servicing processes. The integration with Odoo-based RFID technology offered a
centralized and real-time view of all equipment and boosted production capacity.
What? Want to Review the Demo of the Solution?
Schedule a Free Demo & Consultation